1.Definition and characteristics of integrated servo motor
The integrated servo motor has an integrated servo driver inside, which can directly receive signals from the controller and perform corresponding actions. Compared with traditional split servo motors, integrated servo motors reduce the number of external connection components, reduce the complexity and cost of the system. In addition, due to the integrated design, integrated servo motors also have advantages in performance, such as higher precision and faster response speed.
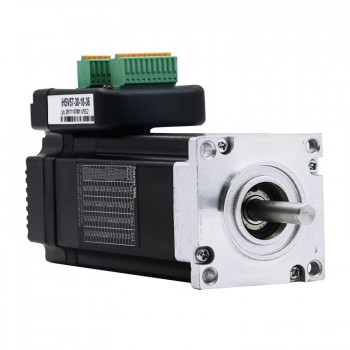
2.Basic working principle of integrated servo motor
When the integrated servo motor receives a pulse, it will rotate the angle corresponding to the pulse to achieve displacement. Since the integrated servo motor itself has the function of sending pulses, each rotation angle will send a corresponding number of pulses, so that the system can know how many pulses are sent to the servo motor and how many pulses are received back, so as to accurately control the rotation of the motor and achieve precise positioning with an accuracy of 0.001mm.
3.Structure of integrated servo motor
1.Stator: The stator is mainly made of laminated silicon steel sheets and is used to fix the magnetic field of the motor. The stator is the stationary part of the motor. After the winding is energized, a rotating magnetic field is generated to provide a power source for the operation of the motor.
2.Rotor: The rotor is usually composed of permanent magnets or electromagnets and is the rotating part of the motor. In permanent magnet servo motors, the rotor has built-in permanent magnets and can generate a magnetic field without external power supply. The rotor begins to rotate under the action of the rotating magnetic field generated by the stator, converting electrical energy into mechanical energy to drive the load to operate.
3.Encoder: The encoder is used to monitor the position and speed of the motor in real time and feed this information back to the control system to form a closed-loop control. Common encoders are photoelectric encoders and magnetic encoders. The encoder is a key component for achieving high-precision control of integrated servo motors.
4.Bearings and end covers: The bearings are used to support the rotation of the rotor to reduce friction and wear; the end covers are used to seal the inside of the motor to prevent dust and moisture from entering. These components together ensure the stable operation and long life of the motor.
5.Controller: The controller is the core component of the integrated servo motor and is mainly responsible for controlling the speed, position and other parameters of the motor. The controller usually uses a digital signal processor (DSP) or a microcontroller (MCU) chip, which has the characteristics of high-speed computing and high-precision control.
6.Driver: The driver is the power source of the integrated servo motor and is mainly responsible for converting the motor's control signal into a motor drive signal. Drivers usually use power semiconductor devices such as MOSFET, IGBT, etc., which have the characteristics of high efficiency and high reliability.
7.Sensor: The sensor is mainly used to detect the position, speed, acceleration and other parameters of the motor, and feed this information back to the controller and driver. Common sensors include encoders, Hall elements, potentiometers, etc.
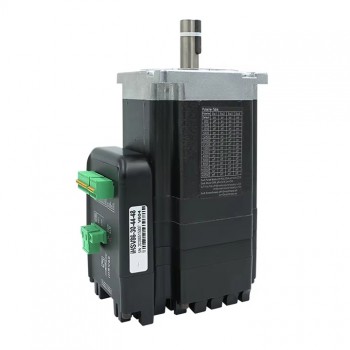
4.Performance optimization method of integrated servo motor
1.Motor selection and parameter adjustment: Select a suitable servo motor according to actual needs to avoid waste or insufficiency caused by excessive or insufficient power. Adjust the motor's inductance, resistance, rotor inertia and other parameters to improve the motor's response speed and accuracy.
2.Optimize the transmission system: Reduce friction and inertia loss in the transmission chain, use low-friction transmission devices and efficient transmission ratios, and significantly improve transmission efficiency. Redesign the mechanical structure, reduce the inertia of components, or optimize the mechanical motion trajectory to reduce the load and thus increase the motor speed.
3.Application of advanced control algorithms: The use of advanced control algorithms, such as vector control, direct torque control, fuzzy control, neural network control, etc., can greatly improve the control accuracy and response speed of the servo motor.
4.Regular inspection and maintenance: Regularly inspect and maintain the integrated servo motor, including cleaning, lubrication, tightening, etc., to ensure that the motor is in good operating condition. Once a motor fault or abnormality is found, it should be handled in time to avoid the expansion of the fault and cause greater damage to the motor.
5.Power supply stability: The integrated servo motor has high requirements on the quality of the power supply, and the power supply voltage fluctuation will directly affect the speed control accuracy and response speed of the motor. Therefore, it is necessary to ensure that the power supply voltage is stable within the rated range, and the power supply waveform can be trimmed by adding filtering circuits.
6.Heat dissipation optimization: In the process of improving the performance of the integrated servo motor, pay attention to the heat dissipation of the motor. By improving the heat dissipation design, such as adding heat sinks, using fans or liquid cooling systems, etc., ensure that the motor will not affect performance due to overheating when running at high speed.
7.Feedback system debugging: It is very important to ensure the accuracy and stability of the encoder or sensor. Perform calibration and inspections regularly to ensure the accuracy of the feedback system and handle any abnormalities promptly.
8.Advanced debugging tips: Use vibration analysis tools to identify mechanical vibration problems and reduce vibration and resonance by adjusting and balancing the components of the transmission system.
Related article:https://www.stepperyoyo.com/2024/09/reasons-for-overheating-of-hybrid.html
Posted
Feb 25 2025, 01:11 AM
by
Amber16