1.What is a servo motor?
A servo motor is an engine that controls the operation of mechanical components in a servo system, and has the characteristics of high precision, high speed and high efficiency. It can convert voltage signals into torque and speed to drive the control object. The servo motor drives the load to move by receiving control signals, and detects the position, speed, acceleration and other parameters of the load in real time through sensors, and feeds back to the controller for adjustment, thereby achieving high-precision control.
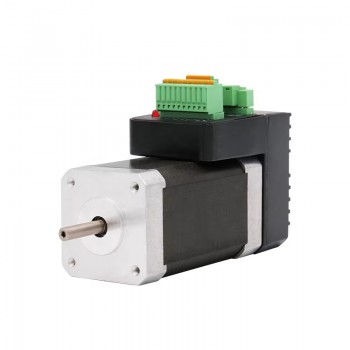
2.Working principle of servo motor
The working principle of servo motor is based on a closed-loop feedback control system, which can achieve precise position, speed and torque control. Servo motors are mainly composed of controllers, drivers and encoders. The controller receives external position or speed instructions and converts them into electrical signals to supply to the motor. The driver supplies three-phase electricity to the motor through a power supply to form an electromagnetic field, so that the rotor rotates under the action of the magnetic field. The encoder detects the position and speed information of the rotor in real time and feeds it back to the driver. The driver compares the feedback value with the target value and adjusts the rotation angle of the rotor to achieve precise control.
3.Servo motor drive mode
1.Position control drive mode: This drive mode controls the object by controlling the position of the motor. Usually, a position sensor is required to detect the position of the motor. Its advantages are high control accuracy, but high cost, and insufficient in instantaneous torque and response speed.
2.Speed control drive mode: The object movement is controlled by controlling the motor speed. The response speed is fast and no position sensor is required. However, it is not as good as the position control drive mode in terms of control accuracy and instantaneous torque.
3.Torque control drive mode: The object movement is controlled by controlling the motor torque. The response speed is fast, and the instantaneous torque and control accuracy are good. However, the torque sensor is required for feedback control, so the cost is high.
4.DC speed control drive: The speed is changed by controlling the voltage and current of the motor. The operation is simple but the control accuracy is low. It is suitable for occasions that do not require high-precision control and positioning.
5.Step speed drive: It controls the number of steps and speed of the motor by providing a pulse signal. It has high positioning accuracy and control accuracy, but the torque is small and cannot withstand excessive loads.
6.Closed-loop control drive: By installing an encoder or other sensor on the motor, the position and speed of the motor rotation are fed back to the controller to achieve precise closed-loop control.
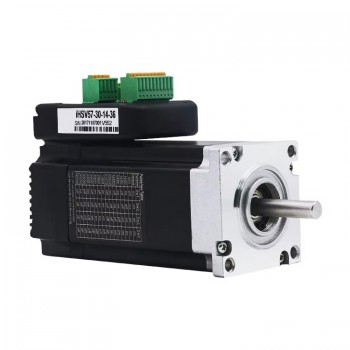
4.Performance debugging method of servo motor
1.Motor parameter setting: Before debugging the servo motor, it is necessary to set the basic parameters of the motor, such as rated voltage, rated current, rated speed, etc. These parameters can usually be found on the nameplate of the motor. The purpose of setting these parameters is to ensure that the motor operates within the normal working range and avoid damage to the motor due to improper parameter setting.
2.Encoder parameter setting: The encoder is an important part of the servo motor and is used to measure the speed and position of the motor. During the debugging process, the encoder type (such as absolute, incremental) and resolution (such as the number of pulses per revolution) need to be set to ensure the compatibility of the encoder and the motor.
3.Speed loop debugging: The speed loop is an important link in the servo system and is used to control the speed of the motor. The proportional (P), integral (I), and differential (D) parameters of the speed loop need to be set to achieve precise control of the motor speed. Usually start with a small value and gradually increase these parameters until the system is stable.
4.Position loop debugging: The position loop is another important link in the servo system, which is used to control the position of the motor. The proportional (P), integral (I), and differential (D) parameters of the position loop need to be set to achieve precise control of the motor position. Again, these parameters should start with a small value and gradually increase until the system is stable.
5.Matching the motor and the drive: It is very important to ensure the match between the motor and the drive. The power, torque, speed and other parameters of the motor need to be checked to ensure that the output capacity of the drive meets the needs of the motor. If necessary, adjust the output parameters of the drive to adapt to the motor.
6.Optimize the transmission system: Reducing friction and inertia losses in the transmission chain, using low-friction transmission devices and efficient transmission ratios can significantly improve transmission efficiency. Redesign the mechanical structure, reduce the inertia of the components, or optimize the mechanical motion trajectory to reduce the load and thus increase the motor speed.
7.Application of advanced control algorithms: The use of advanced control algorithms, such as vector control, direct torque control, fuzzy control, neural network control, etc., can greatly improve the control accuracy and response speed of the servo motor. In particular, model predictive control and adaptive control can automatically adjust the control parameters based on the system model or real-time data to adapt to the dynamic changes of the system.
8.Regular inspection and maintenance: Regularly inspect and maintain the servo motor, including cleaning, lubrication, tightening, etc., to ensure that the motor is in good operating condition. Once a motor fault or abnormality is found, it should be handled in time to avoid the expansion of the fault and cause greater damage to the motor.
Posted
Jan 16 2025, 12:25 AM
by
Amber16