1.Basic principles of hybrid stepper motors
The hybrid stepper motor is designed by combining the advantages of permanent magnet and reactive stepper motors. Its rotor itself is magnetic, so the torque generated at the same stator current is greater than that of the reactive stepper motor, and the step angle is usually smaller. This design makes the hybrid stepper motor perform well in high-precision control.
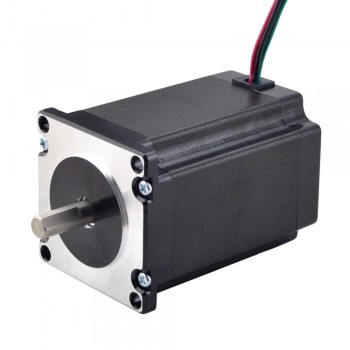
2.Design structure of hybrid stepper motor
1.Stator: The stator is the fixed part of the motor, usually stacked with silicon steel sheets. There are multiple coils wound on the stator to generate a magnetic field. The shape and size of the stator have a great influence on the performance of the motor.
2.Rotor: The rotor is the rotating part of the motor, usually made of permanent magnet material. There are also multiple poles on the rotor, which attract and repel the poles on the stator to generate a rotational torque. The design of the rotor makes the motor produce a greater torque than the reactive stepper motor at the same stator current.
3.Rotor shaft: The component that connects the rotor and the load, usually made of high-strength materials to withstand large torque.
4.Bearing: The component that supports the rotor shaft, which can reduce friction and wear and increase the life of the motor.
5.End cover: The component that protects the internal components of the motor, usually made of metal or plastic.
3.Methods to reduce the risk of failure of hybrid stepper motors
1.Select the right load and driver: Selecting the right load can effectively reduce the resonance phenomenon and prevent the motor from losing steps. If the load inertia is too large, you can consider distributing it to multiple axes or using a reducer to reduce the load inertia. At the same time, make sure that the driver used matches the motor, can provide sufficient current and work stably.
2.Adjust the motor control parameters: By adjusting the motor control parameters, such as acceleration, speed, step angle, subdivision number, etc., the occurrence of resonance, loss of step and noise can be effectively reduced. It is recommended to adjust according to the actual situation to avoid excessive adjustment and other problems.
3.Install dampers and radiators: Installing dampers can effectively reduce the occurrence of resonance and improve the stability of the motor. Installing radiators can effectively reduce the temperature of the motor, avoid overheating, and improve the stability of the motor.
4.Control the motor running time and ambient temperature: Control the motor running time to avoid overheating caused by long-term high-speed operation. At the same time, control the ambient temperature and choose a suitable installation location to avoid the impact of high temperature environment on the motor.
5.Use a stable power supply: Using a stable power supply can avoid the impact of voltage fluctuations on the motor, thereby reducing the possibility of motor jitter.
6.Optimize the acceleration and deceleration curve: During dynamic movement, optimizing the acceleration and deceleration curve can reduce load jitter and improve the stability and service life of the motor.
7.Improve electrical wiring: Try to keep the distance between the control signal and the high current load line or the impact load line. If the electromagnetic environment is particularly harsh, try to use shielded wires or twisted pairs for the control signal line.
8.Choose a stepper driver with sine wave control: If you cannot avoid the natural vibration frequency speed range, try to choose a stepper driver with sine wave control to reduce vibration and noise.
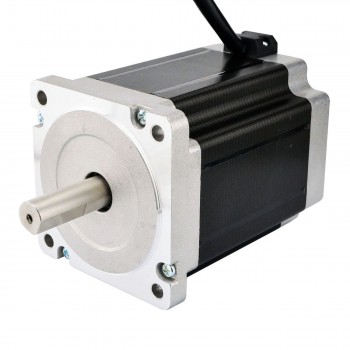
4.Design requirements for hybrid stepper motors
1.Step angle design: The step angle design of a hybrid stepper motor is one of the key parameters. The smaller the step angle, the higher the precision of the motor. Common step angle designs include two-phase, three-phase and five-phase, among which the two-phase step angle is generally 1.8 degrees, the three-phase step angle is generally 1.2 degrees, and the five-phase step angle is generally 0.72 degrees.
2.Subdivision drive design: Subdivision drive technology can achieve step angle subdivision by controlling the current in the stator winding so that the synthetic magnetic field inside the stepper motor changes according to certain requirements. This method can reduce the step angle, improve resolution, reduce low-frequency vibration, and make the motor run more smoothly and evenly.
3.Torque design: The rotor of the hybrid stepper motor is magnetic, so the torque generated under the same stator current is greater than that of the reactive stepper motor, and the step angle is usually smaller. This makes the hybrid stepper motor have better application prospects in situations requiring high precision and high torque.
4.Material selection: Hybrid stepper motors usually use rare earth permanent magnet materials with high magnetic density characteristics as rotor magnets to ensure the high performance and stability of the motor. In addition, the material selection of the motor is also very important. For example, the use of high-temperature resistant permanent magnets and high-quality cold-rolled steel sheets can improve the performance and life of the motor.
5.Structural optimization: The structural optimization of the hybrid stepper motor includes the symmetric design of the stator winding, the neglect of magnetic saturation, eddy current and core loss, and the dynamic response process of the excitation current. These optimization measures can ensure the stability and efficiency of the motor during operation.
Posted
Nov 14 2024, 11:25 PM
by
Amber16